Exploring the Importance of Silicone Membrane for Vacuum Forming
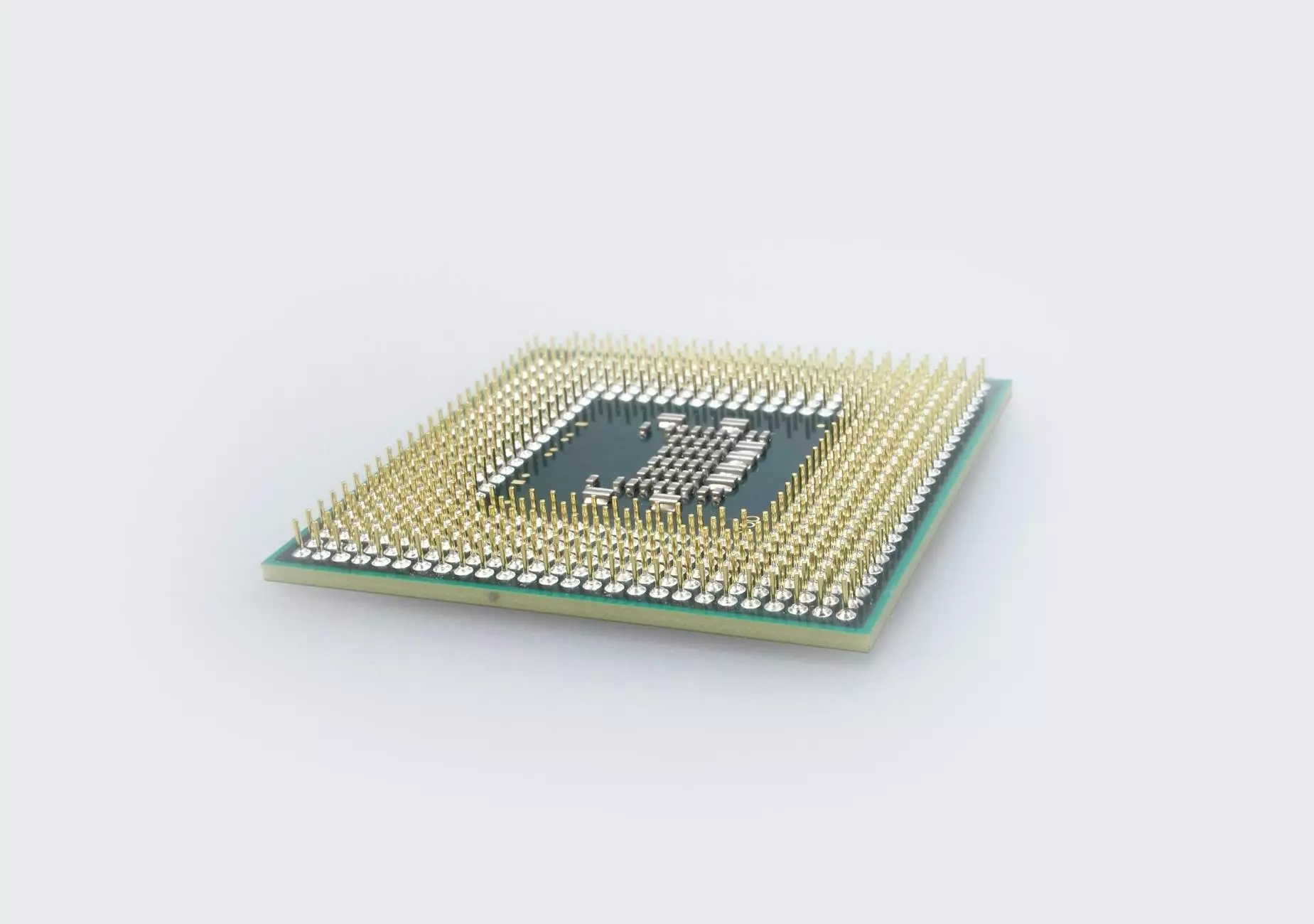
The manufacturing industry has constantly evolved, integrating numerous technologies to enhance product quality and efficiency. One significant breakthrough in this domain is the application of the silicone membrane for vacuum forming, a technique that has revolutionized the way products are shaped and manufactured. In this article, we delve into the intricate details of silicone membranes, their applications, advantages, and why they are becoming indispensable in various sectors.
What is Vacuum Forming?
Vacuum forming is a widely-used process in plastic fabrication where a sheet of thermoplastic is heated until pliable, then stretched over a specific mold and formed into shape using atmospheric pressure. The process is efficient for creating lightweight parts and is utilized across diverse industries, from automotive to packaging.
Key Components of Vacuum Forming
- Thermoplastic Sheet: The primary material transformed into the desired shape.
- Mold: The form over which the thermoplastic is shaped.
- Heating Mechanism: Ensures the thermoplastic becomes pliable prior to forming.
- Vacuum System: Creates suction to pull the heated thermoplastic against the mold.
The Role of Silicone Membrane in Vacuum Forming
A silicone membrane plays a crucial part in several applications within the vacuum forming process. These membranes are specifically designed to enhance the efficiency and quality of formed parts. Typically fixed in place over the mold, the silicone membrane helps regulate the vacuum pressure, ensuring a smooth and consistent forming process.
Benefits of Using Silicone Membranes
Utilizing silicone membranes for vacuum forming provides several advantages that can significantly improve production output and quality:
- Enhanced Durability: Silicone materials possess a high resistance to heat and wear, making them suitable for long-term use in various molding applications.
- Superior Flexibility: The elastic properties of silicone allow it to conform accurately to complex mold shapes, ensuring an exact replication in the final product.
- Improved Air Tightness: Silicone membranes create an optimal seal around the mold, which enhances the vacuum’s effectiveness, leading to better product consistency.
- Easy Maintenance: Silicone is easy to clean and maintain, reducing downtime due to wear and tear.
- Chemical Resistance: This material is resistant to many chemicals, providing longevity in various manufacturing environments.
Applications of Silicone Membrane in Various Industries
The versatility of silicone membranes makes them ideal for several applications across different industries. Let’s explore some of their significant uses:
1. Packaging Industry
Silicone membranes are extensively used in the packaging industry to create secure, durable, and customizable packaging solutions. Their ability to form tight seals is invaluable for products that require barrier properties against external elements.
2. Automotive Industry
In the automotive sector, silicone membranes are used for creating interior components, dashboards, and other intricate shapes, ensuring high-quality finishes with excellent durability.
3. Medical Devices
The medical industry benefits from silicone membranes, particularly in creating devices that demand precision and reliability. Their biocompatibility and non-reactivity make them a preferred choice for medical applications.
4. Electronics Manufacturing
Silicone membranes facilitate the production of complex, lightweight electronic casings and components, enhancing device longevity and performance.
Choosing the Right Silicone Membrane for Your Business
When it comes to selecting the most appropriate silicone membrane for vacuum forming, businesses should consider several critical factors:
1. Thickness and Elasticity
The thickness of the silicone membrane will influence its durability and performance. A thicker membrane may offer more robustness, while a thinner one could provide better flexibility for intricate molds. Balancing these factors according to your specific applications is crucial.
2. Temperature Resistance
Silicone membranes are available in various formulations that withstand different temperature ranges. Businesses should ensure that the selected membranes can endure the heating processes involved in vacuum forming without degrading.
3. Chemical Compatibility
Understanding the environmental conditions in which the silicone membrane will be used is essential. Certain silicone formulations are designed specifically to resist chemical exposure, making them more suitable for specific industrial applications.
4. Customization Options
Many suppliers offer customizable silicone membrane products. Businesses should consider working with manufacturers who can provide tailored solutions to meet their unique production needs.
The Future of Silicone Membranes in Manufacturing
As technology continues to advance, the applications and capabilities of silicone membranes in vacuum forming will evolve. The future promises innovations aimed at enhancing the efficiency and sustainability of manufacturing processes. Manufacturers who adopt these advancements early will gain a competitive edge in their respective markets.
Conclusion
In summary, the role of silicone membranes for vacuum forming cannot be overstated. Their distinctive properties contribute significantly to the efficiency, quality, and versatility of vacuum forming processes across various industries. As you consider the optimal solutions for your business, understanding the comprehensive benefits of silicone membranes can guide your decision-making, ultimately leading to improved production outcomes and product excellence. Companies like vacuum-presses.com are at the forefront of providing high-quality solutions that can help you stay ahead in the rapidly evolving business landscape.